How to reduce downtime in manufacturing?
Downtime in manufacturing leads to operational inefficiencies and financial losses. You could reduce downtime, even for short periods using automated processes, IoT and predictive analytics, real-time monitoring and maintenance, and Industrial 4.0. Read the blog to learn more in detail about how to fix this critical problem in the manufacturing industry.

Ram
Oct 23, 2024 |
9 mins
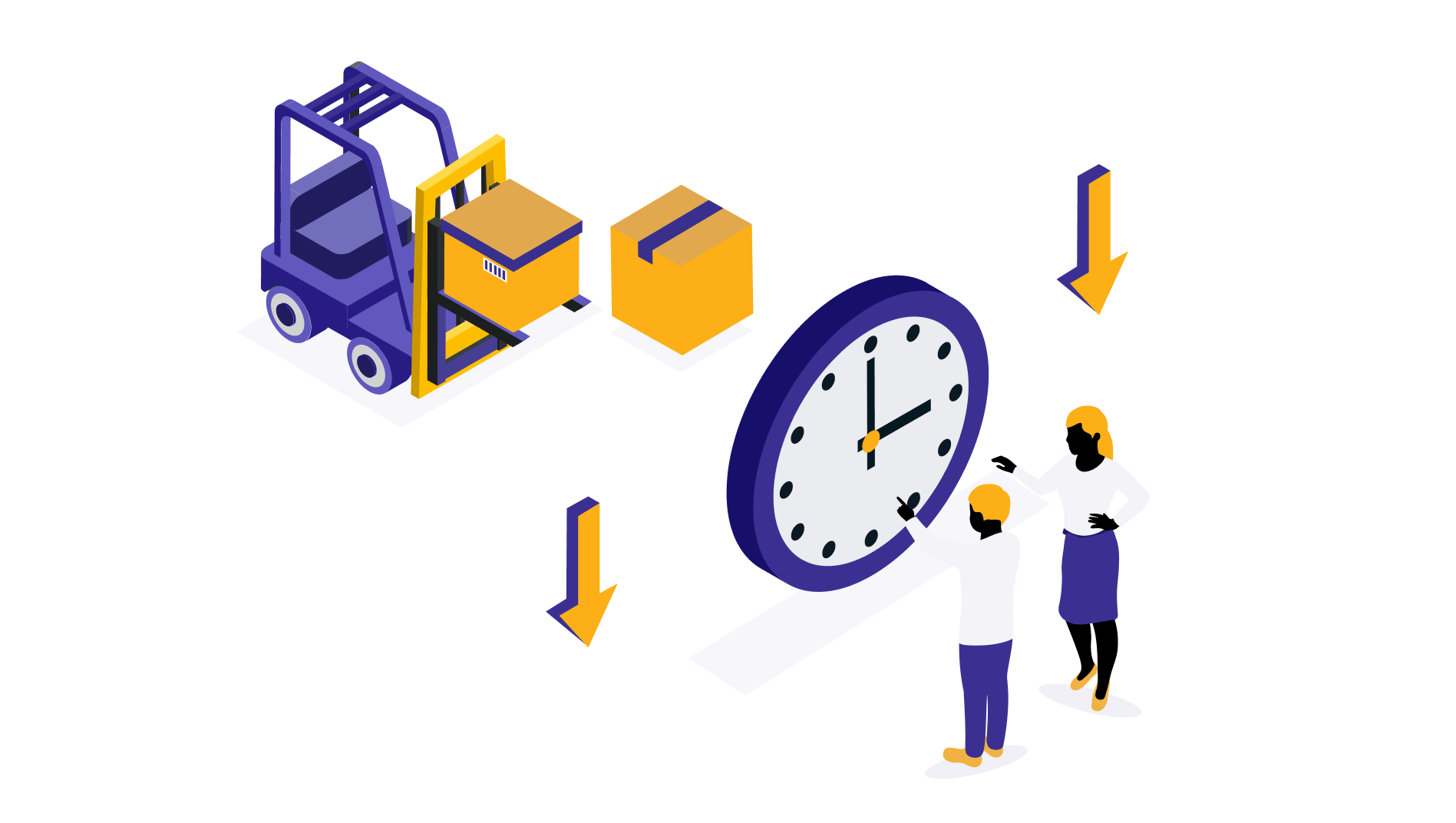
What is downtime and its types?
Manufacturing downtime is the production interruptions and delays caused due to machinery breakdowns, software failures and updates, equipment replacement, and failures. Downtime is measured in time period and it's the duration where there is no production activity happening. Downtime can be both planned and unplanned, but both are unproductive, which results in low output, reduced efficiency, and increasing costs.
There is a way to measure downtime using a formula.
Downtime in % formula = total downtime/available production time * 100
Let’s say that your machinery downtime is 20 hours per week and uptime is 100 hours per week. Then your downtime% will be 20/100 = 0.2 * 100 = 20%.
Types of downtime
Planned downtime: non-operating time scheduled in advance done for purposes like machine calibration, equipment replacements, software upgrades, etc.
Unplanned downtime: downtime happening due to unforeseen circumstances like power disruptions, outages, machine breakdowns, and technical issues. Example: conveyor belt blockages or seized rollers.
Maintenance downtime: a type of downtime to give rest to continuously operating machines, which could be both planned or unplanned. Manufacturing units perform this type of maintenance to keep machines running in optimum conditions.
Supply shortage downtime: when production works stop due to lack of raw materials and supplies, which can happen due to supply delays or poor planning.
Labor shortage downtime: downtime that happens due to insufficient laborers who could handle the machinery.
IT downtime: downtime caused by malfunctioning of IT or IoT systems, digital control panels, system updates, or other technical glitches.
7 ways to reduce downtime in manufacturing
Downtime can be of many types. But they all are interruptions you could prevent. Here are seven proven ways to reduce downtime in manufacturing.
Calculate your downtime
Solving a manufacturing industry problem requires data and root cause analysis. So, start with a detailed report of how much time you lose due to downtime and maintenance activities. Perform root cause analysis to find out the underlying reasons for interruptions. This can help you set up preventive measures to stop similar problems rising in the future.
Based on findings, you could assign solutions for each problem. For example, investing in and replacing spare parts, creating a new schedule for lubrication, or identifying the faulty component.
It can be hard to note down and calculate downtime accurately. Use downtime monitoring dashboards for automated monitoring and assessment. This is the first step towards reducing downtime in manufacturing operations.
Automate process
Automating maintenance processes can reduce downtime and make it more efficient without burdening the involved teams. Automation brings in periodic and timely scheduled updates, preventing oversight, human errors, and inconsistent monitoring.
It can trigger automated alerts to technicians on time and allocate sufficient resources.
Here are the benefits of automated maintenance systems.
Increased accuracy and consistency, where there are no human errors.
Real-time monitoring and feedback implementation, all tracked through centralized systems.
Continuous monitoring ensures that there are no unplanned downtimes or failures.
Teams involved could focus on other critical tasks and worry less about machinery performance.
Proper data collection and analysis leads to timely root cause analysis, when there are defects or performance issues.
Can scale up or down production, meeting customer demands smoothly and maintaining quality 4.0 standards.
Preventative maintenance
Many manufacturing companies today perform corrective or reactive maintenance, where they inspect machines only when it’s struggling to perform. And then there is scheduled maintenance, where equipment is checked periodically in a repeated manner.
While the above types of maintenance schedules work for most, preventive and predictive maintenance has more benefits to offer. This is for companies aiming to maximize machinery lifespan with minimal repair time, as scheduled maintenance also leads to downtime.
To achieve preventive maintenance, you can utilize data analytics solutions and monitor machinery data like speed, heat, emissions, and other health factors. By measuring them, you can know in advance when the machine's working conditions deteriorate.
Here’s how preventive maintenance directly impacts downtime.
Reduce the need to perform scheduled maintenance and thereby periodic downtime.
Alerts when machine conditions require inspection and care and prevent unplanned downtime.
Fixing before it gets worse reduces the time required to operate.
Continuous monitoring ensures optimal running, which enhances the machine's lifespan and prevents downtime.
Take advantage of your data
Manufacturing industry deals with abundant sources of data coming from production lines, supply chain, IoT and other tracking devices, and customer/vendor details. Some companies have data teams that send periodic reports to business users, highlighting monthly, weekly, or annual performance and other statistics. These reports are useful and handy, but they could be more effective if the company utilizes data analytics fully.
Here are the ways the manufacturing sector can take advantage of data to reduce downtime.
Setting up real-time data monitoring systems to track machines 24/7 and its operational data like RPMs, heat levels, or pressure.
Optimize process and make immediate changes based on real-time data. For example, increased heat levels could denote machine overburdening. Stopping operations for a while or reducing the load as soon as the team receives alerts.
Use data and analytics root cause identification required to prevent recurring issues.
Use cloud-based platforms and storage systems to collect, process, and analyze data without interruptions.
Use data visualization platforms like Power BI and Tableau to receive customized visual reports that compare trends over time of indicators like equipment uptime, utilization rates, and maintenance status.
IoT and Industrial 4.0
Internet of Things and Industry 4.0 play a huge role in reducing manufacturing downtime across departments. Here’s how manufacturing teams use IoT to enable proactive maintenance and reduce downtime.
Set up IoT, sensors, and connected devices to monitor equipment performance and collect data like temperature, vibration, pressure, energy usage, etc.
Combine IoT data with data analytics, cloud computing, and augmented analytics to adjust production speeds, load balancing, and even start self-maintenance tasks.
Use AI and predictive analytics to read machine patterns, predict future performance, auto-schedule maintenance at non-peak hours, and receive other mandatory insights.
Identify early signs indicating machine wear and tear and send automated alerts to concerned teams.
Maintain machine health remotely and receive health-based alerts, even when the technician is not physically present.
There are other evolving technologies, like digital twins and simulation models. Digital twins allow manufacturers to create a virtual working model of their factory, perform experiments, and observe results without causing risks and delays to real-world production. Example: A manufacturing plant using simulation to create virtually the production floor, test how different workloads impact the wear and tear of the conveyor, and find out the ideal workload.
Train and educate teams
Some key reasons for downtime in manufacturing are labor shortage, poor operational awareness, and skill gaps. It requires the following measures by the manufacturing companies to curb downtime through awareness programs.
Educate employees and users with enough technical knowledge required to operate the machines.
Conduct retraining programs and live workshops to help users find out root issues and perform simple fixes by themselves.
Cultivating a culture where employees take responsibility and accountability for not only their work but also keeping the machinery running in good conditions.
Create and nurture data-driven teams that stay on top of real-time maintenance updates and act on it immediately. Also, employees must be willing to be a part of tech-driven production processes, which also involve working with IoT, AI, data and BI systems, edge computing, and digital twins.
All these things will ensure that you work as a team to ensure high operating time and low to zero down time in your manufacturing unit.
Benefits of having planned downtime
Not all manufacturing downtime is bad for the production output. Equipment and gears still need to be in the rest position for idea operations. That’s where planned maintenance comes in. By combining predictive maintenance insights with maintenance scheduling, you could avoid unnecessary, interruptive, and expensive downtime, achieving production goals and improving equipment efficiency.
Here are some benefits of having planned downtime.
Prevents unnecessary breakdowns that could lead to expensive failures and long non-operational hours.
Protect workers and other machinery from safety hazards.
Improves machine efficiency, outcomes, and overall equipment effectiveness (OEE), promoting manufacturing cost reduction.
Helps with sustainability measures by reducing emissions and fuel intake.
Planned downtime also helps with better resources planning and allocation.
Give time to perform any necessary upgrades or improvements.
Final thoughts
The manufacturing units could reduce downtime and increase productivity by three ways - refining processes, using data analytics, AI, and advanced tech, and educating workers to adapt to the above. By ensuring all the above points, you could reduce maintenance costs, maximize operational efficiency, and eliminate any production interruptions, which are crucial for new-age manufacturers.