How to improve manufacturing productivity?
Looking for ways to improve manufacturing productivity and efficiency? Find out the simplest ways to achieve this with the help of data, analytics, and AI. Learn how the three can transform the core elements of your industry - people, processes, and equipment efficiency, getting the best from all.

Ram
Nov 9, 2024 |
8 mins
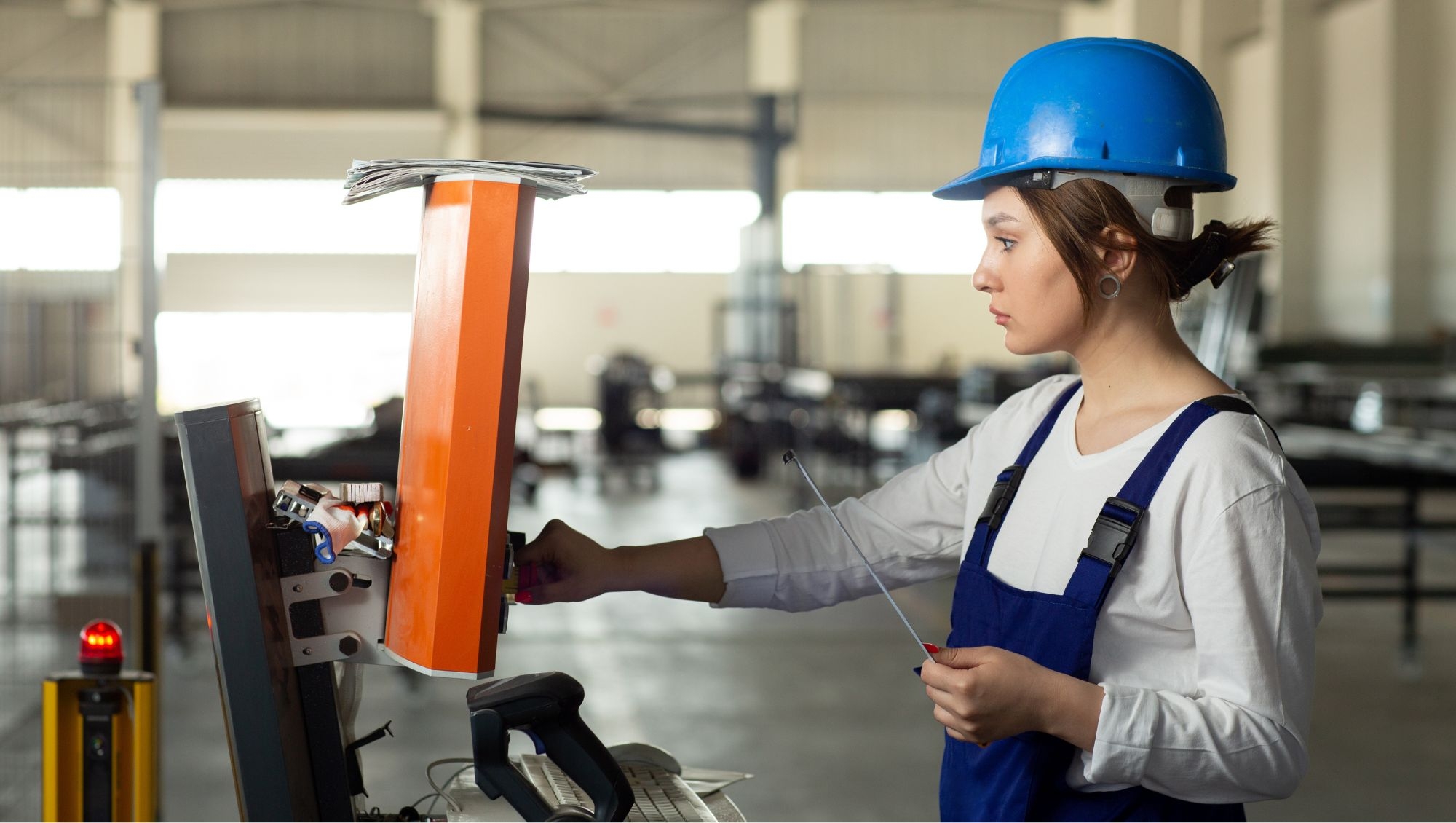
Importance of improving manufacturing productivity
Productivity means much more than employee work outcomes. For the manufacturing industry, it denotes the combined effort from people and other resources that makes the manufacturing process so efficient. Think about this - achieving production schedules with better resource utilization and low operational costs. That’s what manufacturing productivity does for your business. Some other reasons why it’s important are:
1 - High productivity means fast turnaround times. You could meet customer demands, even if it changes every day or hour.
2 - Use resources and assets better, while aligning everything together with production goals and labor availability.
3 - Scale up operations smoothly without being affected by issues like market disruptions, economic downturns, increased competition, etc.
4 - More clear processes and goals and fewer bottlenecks leading to a stress-free work environment for workers, which improves employee satisfaction.
5 - Highly productive manufacturing units demonstrate more profitability and stability and attract further growth and investment opportunities.
Ways to improve manufacturing productivity
Improving production efficiency and outcomes call for measures like automation, implementation of advanced technologies like lean manufacturing or JIT inventory management, and above all, optimized workforce management. Let’s see some ways you could achieve enhanced productivity in the workplace.
1. Educate and train your employees
Improving manufacturing productivity starts with employee education and training programs. Implement the following measures to see a direct impact on productivity.
Cross train employees to learn beyond their roles and responsibilities to make them more flexible and collaborate better.
Certification and accreditation programs to help them pursue relevant skills and LMS systems to track progress.
Fun activities like role playing, problem-solving exercises, or observing simulations when they must be trained on complex skills.
Peer learning programs and knowledge sharing platforms for them to open up, mingle with others and learn.
Overall, promoting a culture of learning and continuous improvement among employees can foster highly productive environments. Such training activities are beneficial for manufacturing companies where employees should be always adaptable to new things.
2. Improve communication and transparency between teams
To make the manufacturing process more efficient, there must be open communication and transparency among employees beyond traditional team structures. This is what can align everyone’s effort, ruling out room for misunderstandings, which could lead to expensive mistakes.
Typically, manufacturing units have stand-up calls and cross-functional teams get together to discuss everyone’s goals, bottlenecks, and overall progress. However, to unlock the highest levels of productivity, these teams require the following:
Use centralized platforms, tracking systems, and project management applications, so everyone can be aware of specifics of ongoing tasks.
Maintain clear documentation for role clarity, so there are no misunderstandings among team members.
Regular check-ins to clear out any concern and one-on-one sessions to hear out each individual’s perspective. Promoting active listening and empathy for employees to reduce any work related stress or tension that stands in the way of a productive work environment.
Standardize communication across teams with defined channels. Employees must know where to look for and who to check with when they encounter any issues.
Recognizing milestones and minor achievements publicly to encourage everyone to deliver better.
Quick protocols for conflict management and resolution that equip teams with better soft-skills, effective communication, and resolution-finding mindset—prerequisite for healthy work environments.
That’s how you build cohesive manufacturing teams that could keep issues away and focus more on work.
3. Machine maintenance
Employees could be productive; but what about unplanned machinery downtimes? It could affect the schedules and cause poor labor utilization. That’s where corrective and predictive maintenance schedules are necessary. Here are the ways to ensure better maintenance planning, which will not interfere with production schedules and labor availability.
Set up IoT systems like sensors that collect machinery health data (temperature, speed, heat, CO2 emissions, etc).
Use machine learning models and data analytics to read inferences from the IoT devices.
Compare the trend values and get automated alerts when machinery vitals demand attention.
Use future-based insights generated from the model to predict potential downfalls and schedule maintenance or break in advance. Align machinery availability with employee shift timings and production schedules.
This is how predictive analytics work for machinery maintenance. You could use this for any kind of equipment - motors, conveyors, power backups, or any other operating systems whose uptime is required for operations.
4. Reduce production costs
Reducing production costs could lead to improved workforce efficiency in many direct and indirect ways. For example, you could use the saved capital and invest it in employee development, facility enhancements, or any other high-value tasks.
But, it’s easier said than done, as production costs always find a way to spike than planned. Here’s how you could reduce production costs and use them to improve employee productivity.
Optimized resources usage by following energy efficiency practices or lean manufacturing methods. Both of these aim to reduce raw material and power consumption costs.
Predicting customer demand in advance using demand forecasting. Operations managers most commonly deal with which type of forecast to reduce overproduction instances, relying on historical data to generate future demand reports.
Focus on inventory management and using methods like Just-In-Time inventory, where you only buy materials when it’s needed, freeing up holding costs and storage.
Use preventive maintenance and analytics to prevent costly equipment repairs, breakdown, and replacements.
Use vendor management analytics to track vendor performance and costs to negotiate better.
Identify sources of wastage to reduce or re-purpose them, which is both a sustainable and a cost-effective practice.
5. Leverage AI
AI can help manufacturing companies in many ways, from automating labor-intensive tasks to optimizing workforce scheduling. Here’s how you could use AI for better manufacturing and labor management tasks if your goal is to improve productivity.
AI-driven automation to handle data entry tasks, inventory updates, reporting, etc., freeing up employees to focus on more important tasks. Using process automation and AI-powered robotic systems for handling hazardous materials or performing laborious activities like lifting heavy objects.
AI-powered scheduling tools for skill matching, labor assessments, and workforce allocation, depending on real-time demands.
Custom-designed chatbots that can help laborers find answers for field or equipment related queries.
Accurate demand forecasting to know granular details of customer requirements - what’s needed, in what quantities, in what specifications, etc..
Fast decision-making with the help of data-driven insights and AI-driven reporting systems, where one could not just view trends, but also ask questions in natural language and get instant answers. For example, answers to specific questions within reported data like, ‘What’s the inventory wastage cost due to expired goods for the third quarter, 2024?’
Ability to perform what-if analysis and simulations to receive better understanding of the current situation, test different scenarios, observe outcomes, and select the best solution.
6. Implementing automation
Implementing automation is the easiest way to improve manufacturing productivity as it frees up employees’ time and effort from trivial activities. Task and workflow automation also reduces time spent on these activities, while minimizing any possible human errors. Here’s how automation could free up your resources’ time, while getting the job done.
Automated quality checks, where using computer vision and AI for detecting defects, reducing human oversight and improving quality control in manufacturing.
Consistent task executions without human interventions, reducing oversight errors and reworks.
Automated notifications and updates, be it task status or reporting, enabling less manual communication and fast decision-making.
Enhanced decision making with real-time data insights, as automated data collection and processing happens.
Automated training and onboarding, especially for temporary employees, so managers don’t have to work or follow-up on routine training sessions.
Robots and automated machinery to reduce physical strain and get jobs done faster and safer.
Employees don’t have to worry about repetitive, time-consuming tasks and could focus on complex problem solving, learning, and contributing productivity to core production tasks.
7. Waste reduction
Waste is clutter, which could be a distraction in production units. Keeping the waste away, reducing them, or streamlining waste management can help employees execute tasks fast without dealing with clutter.
Manufacturing waste could be of many types - overproduction, excess inventory, packaging, non-operating equipment, etc.
Here’s how manufacturing companies could deal with waste and prevent it from becoming a productivity hindrance.
Following lean manufacturing methods, which focuses on minimal or just-the-needed resources and inventory, while allowing room for consistent progress.
Tracking inventory levels in real time, so you could identify fast-moving raw materials and order right on time without overstocking or out-of-stock issues.
Dealing with eco-friendly and easy-to-handle packaging materials that one can easily store, manage, and dispose of.
Setting up preventive maintenance to increase equipment effectiveness and lifetime, which leads to fewer breakdowns and failures.
Final thoughts
Improving manufacturing efficiency and employee productivity is essential for manufacturing companies to stay resilient and thriving. With a few targeted and mindful activities like inventory tracking, predictive analytics, automation, equipment maintenance, and transparent communication, the industry could easily improve employees’ work nature and productivity.
However, it can be daunting to reform everything in one day. That’s why we help our clients start small by streamlining their tracking using analytics solutions and dashboards. The path becomes much clearer from here, as you integrate siloed departments, bring visibility to their combined progress every step of the way, and pave a shortcut to achieving industry 4.0 and automation vision.
Check out the story of how our client achieved lean manufacturing using inventory analysis, making a huge difference in wastage, cost savings, and employee productivity.