Quality 4.0 for manufacturing: What is it and reasons to implement
The manufacturing sector has leveled up its quality standards from Quality 3.0 to Quality 4.0. What does this mean for the quality teams and how can they perform data-driven quality management, where they foresee quality issues before they happen, while saving time, cost, and effort?

Ram
Oct 14, 2024 |
10 mins
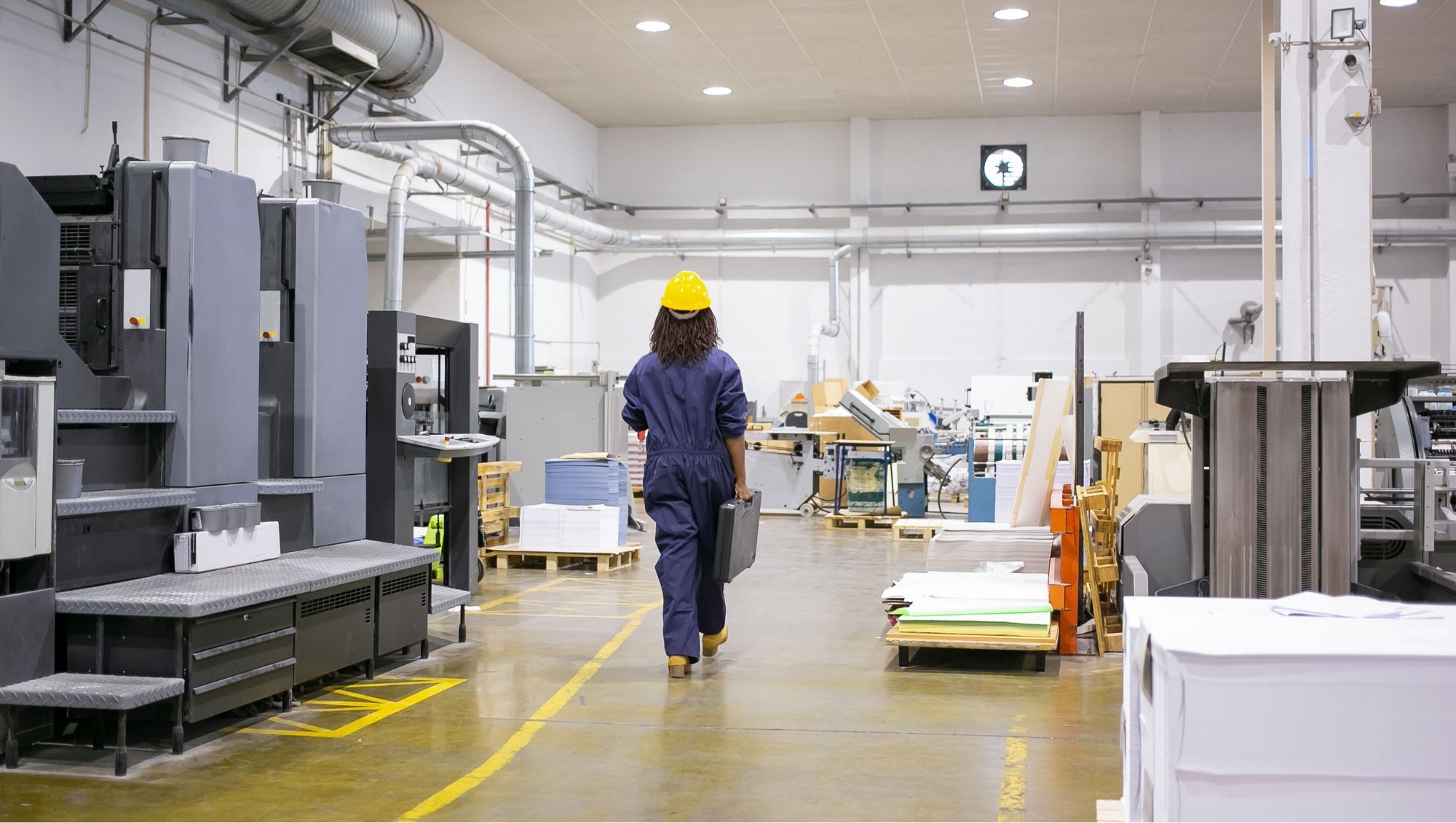
What is Quality 4.0?
Quality 4.0 is the intersection of people, technology, big data and analytics to automate quality management, get actionable insights from real-time data, and build a flexible, responsive, and highly efficient quality control process.
With the help of advanced tools like IoT and sensors and real-time data management systems, you ensure continuous monitoring, prediction, and prevention of quality issues across manufacturing and supply chain.
Key elements of Quality 4.0
IoT and connected devices: Interconnecting sensors, machines, and other devices from produce to supply chain and collecting data from all quality touch points.
Data processing and management: organizing collected data and standardizing them for extracting information, while ensuring data security and governance.
Advanced analytics: using predictive and prescriptive analytics solutions to read behind the data, predict any possible downtime, failures, or deviations from standards, and alert respective teams for a quick fix.
Cultural transformation: Aligning people, company culture, and leadership with the new way of working, from adopting advanced technologies to incorporating predictive and prescriptive analytics into their work to making agile and proactive changes and decisions to make autonomous quality management happen.
Quality 4.0 is more about technology and data. It’s a digital transformation process that breaks silos down between manufacturing, quality, inventory, and IT and data, while aligning everything with customer demands.
Quality 4.0 evolution
Quality control in manufacturing has gradually evolved over the years, from manual methods to data-driven, automated processes. Here is a summary of stages of Quality evolution.
1. Traditional quality management: No impact of technology and quality control entirely dependent on skilled workers and craftsmanship. Low production ranges and standards were even lower, yet there were inconsistencies and mismatch due to the manual work, leading to high error rates, waste, and poor quality.
2. Mass production: Growth of assembly lines and mass production, marking the second phase of the industrial revolution. Statistical quality control (SQC) brought into practice, to identify defects, maintain standards, and make reactive changes. Periodic quality checks happened, though data collection and analysis were all manual.
3. Introduction to ISO and TQM (Total Quality Management): Manufacturing industry meets global ISO quality standards, which involves continuous monitoring, employee involvement from all teams, QMS tools and systems. The systems were semi-automated, improving quality adherence, but they had no predictive power, nor could they act on real-time information, as most manufacturing units had siloed data.
In later parts of this era, around the late 20th century, the industry got its digital QMS and ERP systems. Automated data collection from systems promoted fast quality reporting and monitoring, but data silos were still a problem, which limited transparency.
1 - Connected QMS systems: The evolution of IoT happened along with cloud computing and automated monitoring systems, which allowed real-time data collection directly from machines and centralized for cross-departmental collaboration. This is the early Quality 4.0 phase, where real-time data integration and analytics happened. However, the quality management and control was not predictive yet.
2 - Predictive quality & Quality 4.0: This is the most recent step change in the manufacturing sector, which integrates fully AI, big data, IoT for autonomous and agile quality control. These systems connect supply chain, procurement, customer feedback, and every other point to predict quality issues before they occur, bringing end-to-end traceability.
3 - The most recent additions to Quality 4.0 are advanced tech like digital twins and self-learning AI, where replicas of real systems help quality professionals run simulations, conduct testing, and improve performance. While this is still under improvement, it can bring zero-defects in the production, ruling out any cost or production wastage.
Quality 4.0 principles
The major pillars of Quality 4.0 are people, processes, and technologies.
1. People
Implementation of quality 4.0 requires cultural drive and alignment from people. Here’s how people play a role in Quality 4.0.
Adoption of data and tech tools and skill development to work with AI, IoT, big data, and augmented analytics. Quality 4.0 also requires cross-functional collaboration among departments like R&D, customer service, supply chain, and production.
While tech might share predictive insights, human insight is still required to interpret data and act on them for autonomous quality management.
2. Process
Quality 4.0 isn’t for the quality department alone. Hence, workflows and processes must be in place to shift from traditional quality management. Here’s how the process plays a role in Quality 4.0.
Connecting manufacturing and quality control end-to-end requires processes that are adaptable for each stage and people involved. These processes must be flexible, streamlined, and agile in nature for continuous improvement. Every company must have their own risk and compliance requirements, and processes must be in line with these.
Set the process, its goal, how to perform & tools used, and which teams will be involved. Examples of a Quality 4.0 process include:
Setting up real-time product defect inspection using RPA, AI, and machine vision.
Adopting the Kaizen process for better efficiency and product quality over time.
Data sharing and access practices within a team and across the team.
Customer feedback integration into product development to close the loop and encourage continuous improvement.
Automating compliance report capturing for seamless audit trails.
And similar industry-related processes like this.
3. Technologies
Technology plays a huge role in connecting the above blocks in Quality 4.0. Common tools and technologies used in Quality 4.0 include:
Big data analytics: Big data and analytics are required to collect, process, and interpret vast amounts of data from manufacturing points. It could be data from machinery, supply chain, QC systems, ERP, customer feedback, or anything related to the quality process. With the help of advanced analytics, you could turn data points into useful insights that the team could work on.
AI and machine learning: AI and machine learning can enhance the quality, accuracy of insights, helping you understand the root-cause of defects and quality issues.
Cloud computing: Helps you have a centralized storage to collect, process, and store data from all sources and from all locations in the cloud.
Digital twins: Digital twin is the virtual simulation of a real-time environment, which you can use to test, predict, make adjustments, and measure its impact before the plan hits the floor.
IoT: IoT refers to the internet of things which helps with real-time data collection from manufacturing and distribution equipment. Example: data from devices like temperature, pressure, speed, heat generation, etc. with the help of sensors and trackers.
Blockchain: Blockchain technology helps with end-to-end traceability, allowing safe and secure data integration and ensuring consistency across all users. It’s also important for manufacturing and supply chain workflows to prevent counterfeits by providing unique identity to every product as it moves across the supply chain cycle. For example, consider a luxury bag brand with a unique RFID tag carrying its details and linked to the blockchain ledger. Be it the customer, distributor, or anyone handling it could validate its details, manufacturing story, and authentication, scanning the code.
Augmented reality: Augmented reality is often used to provide immersive and interactive experiences in a virtual environment. You could use augmented reality to help the workforce with learning and skill development, guided maintenance process, remote assistance, and visual quality inspections.
Why should you implement Quality 4.0?
Pick any quality issue—poor packing, imperfections, incorrect assembly, or missing parts, one defect could cause consistent damages and rejections until the root cause is identified and fixed. Example: a conveyor belt issue causing improper packaging of goods leading to damages during transportation. It’s evident that these quality issues are expensive and complicated to deal with.
On the other hand, there is varying product demand, dynamic manufacturing requirements, raising customer expectations and quality standards, and, on top of all, cut-throat competition. It can be highly difficult to rely on manual quality control methods for any manufacturing and supply chain unit fighting with the above battles. Integrating Quality 4.0 can be the starting point to bring quality problems under control and reduce chances for costly reworks.
Benefits of Quality 4.0 for your business
Predict and prevent issues before they become product defects and make proactive changes in quality management.
Real-time analytics for improved decision-making that drive expected results.
Complete traceability of the product throughout its lifecycle, with every quality aspect neatly documented to meet compliance requirements.
Improved efficiency and speed, where workers could work fast without fatigue, being able to focus more on high-value tasks.
Ability to deliver exceptional quality products that meet market and customer expectations, also bring in customer feedback into product development.
Fine-tune existing processes and make step-level improvements to enjoy long-term benefits.
Final thoughts
Quality 4.0 is more than just a set of advanced technologies—it's a shift in mindset that brings people, process, and technology together. While the allure of AI, IoT, and automation might suggest a future run entirely by machines, the reality is far more human. Imagine walking the shop floor and being able to visualize every machine’s performance, predict issues, and ensure that every product that rolls off the line is of the highest quality. That’s what quality 4.0 can help you achieve.
It’s all making data-driven decisions not a buzzword, but a part of daily life and fostering a culture of continuous learning and improvement.