A definitive guide on Logistics inventory management
An all-inclusive blog that discusses the pressing inventory management problems of the logistics industry, from tracking to stocking, along with practical solutions. Find how you can put your data to good use for smooth inventory management in logistics.

Jagadeesan
July 21, 2024 |
8 mins
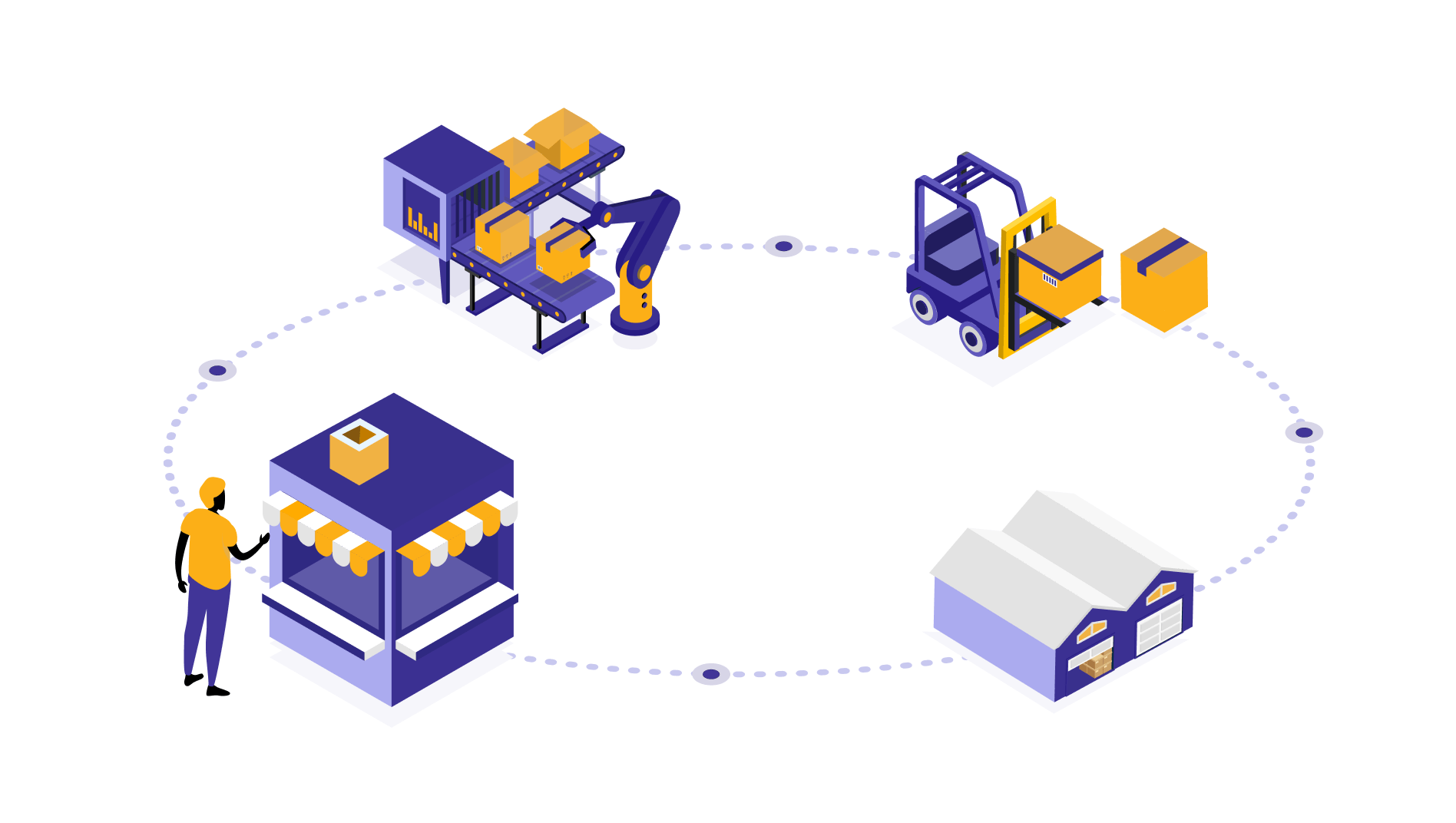
What is logistics inventory management?
Step into the world of eCommerce and fast shopping, where you can have whatever you desire in a jiffy - whether it's some exotic herb or a local gem. But the backbone of it all is the always buzzing and well-planned logistics and inventory activities. It takes a well-managed inventory to meet their customers’ demands and supply them on time, without going out-of-stock or wasting because of overstocking. This process of maintaining inventory in ideal levels to meet erratic demands, while dealing with complex supply chain issues and other challenges, is what we call logistics inventory management.
Companies like Amazon and Walmart use data, analytics, and ML to tackle inventory and distribution management challenges. They predict demand, optimize inventory based on real-time requirements, and streamline the entire supply chain at reduced costs. It shows how data is imperative to sustain and keep up the flame of modern consumerism.
Logistics and warehouse managers, take notes as we spill more secrets into successful inventory management using data analytics.
Challenges with inventory management
The current landscape is a bit tricky for logistics and inventory managers. Here are some challenges they deal with every day.
Manual process and tracking
Using manual records and processing entries with pen and paper, that’s like living in the 90s. While it can be convenient for some, it’s also time-consuming and labor-intensive. There are high chances for incorrect or missed entries, inaccurate data, leading to stock discrepancies, delayed manufacturing, or missed sale opportunities. Also, the lack of transparency makes it difficult to align the inventory numbers with current demands. Finally, if the inventory head must send a summary or report, they will have to deal with the fragmented data again, making it more inefficient than it is.
Warehouse space management
Spacing is a growing problem in inventory management in logistics, causing disorganized storage, misplaced items, and time-taking complex tracking. Without knowing the exact demand, warehouse workers struggle with storing stocks in optimal positions. As they don’t know the time-in and time-out of stocks, they are unable to focus on optimizing storage, no matter how favorable their warehouse layout is.
Such unplanned warehouses can also become unsafe for laborers with poor aisle spaces and gregariously stacked up stocks, while also leading to materialistic damages.
Customer demand
Holidays, seasonal changes, special campaigns, personal tastes and preferences and so many other factors could impact customer demand. While businesses get the gist of a few of them, it cannot tell them exactly what products are in demand and how many will they sell. This can be a headache in inventory management, given that every product comes with a shelf-life.
Storing product variations to supplying varying demands of each variation to handling their pick and pack on time, everything requires mammoth efforts.
So, predicting accurate customer demands and storing and optimizing the warehouse inventory is the need of the hour for modern logistics companies.
Overstocking and understocking
Both overstocking and understocking are situations to be avoided as they lead to wasted stocks or sale opportunities. Overstocking the inventory ties up your capital in one place and comes with the risk of aging stocks and potential write-offs. Whereas, understocking drives customers away as the inventory cannot supply them on time. For ideal inventory management, it takes stocking only the required product in required amounts.
Remember the tragic failure of Target expansion into Canada in 2015? One reason they failed is due to poor stocked racks and taking too long to replenish missing products. These supply chain challenges, combined with many problems, led them to close all of their 124 stores in the country despite their great marketing efforts and discounts.
Inventory management techniques
Dropping some inventory management techniques followed by top logistics, retail, and CPG companies below.
Just-in inventory
Mainly for companies that produce products on demand, Just-in inventory is ordering supplies just when they are required. This would leave manufacturers with just the needed raw materials required to meet production volume and customer demands. So, there won’t be excess inventory lying around, wasting resources and tying up production costs. In certain cases, it minimizes the need for an inventory, allowing the vendor to ship directly the supplies to the assembly area. While the concept can appear interesting, it also demands forecasting your requirements with precision. Otherwise, it can lead to operational chaos, vendor disputes, and stock-out issues.
The legendary automobile company, Toyota, uses this technique for lean manufacturing and reduced warehouse costs.
ABC analysis
This is a highly effective inventory management technique for warehouse spaces handling a huge number of products. It helps to prioritize storage units based on categories the product falls under. Here is how the categorizing works.
A - High-value products that sell in lower volumes
B - Medium-value products that sell in mid volumes
C - Low-value products that sell in large volumes
This requires listing down all inventory products, their consumption volume, price, and annual sales. Sorting the items based on the price and sales will help you establish the following.
20% of high value items that lead to 80% of inventory value
30% of medium-value items that contribute 15% of inventory value
The remaining items that contribute to the remaining 5%.
Estimating this will help you shift the required focus to each category to bring the maximum value to the inventory. It also helps the business ensure that the critical items are always in stock, while allocating the right storage for each category product.
FIFO and LIFO
FIFO is First-In, First-Out is the concept of selling the oldest products of inventory first. LIFO is Last-In, First-Out is the concept of selling the newest products of the inventory first. Both have their benefits and are suitable for certain types of businesses. FIFO is best suited for logistics companies dealing with perishable and time-bound goods. By sending out the old stocks first, they could prevent waste due to expiry.
LIFO gains tax advantages for businesses, identifying and selling the most promising, high-cost items at low tax incomes, especially during inflation times. It also eases the accounting process, where you can match accurately the cost of goods with profits in an inflationary economy.
Both methods bring harmony and organization into the inventory management, helping businesses close with maximum inventory value at higher efficiency.
Batch analysis
This involves sorting inventory stock into batches based on any one of its characteristic traits. Each batch is given its identity, which is used to track the stock throughout the cycle. This is great for inventory management of grocery chains and perishable goods, where every product comes with distinct ingredients, manufacturing date, shelf life, storage restrictions, and more. In such cases, it becomes particularly helpful with quality control and expiration management and not letting non-consumable products to shelves.
Drop shopping
This is a common inventory management technique used by modern eCommerce businesses. Here, the customer places an order, the business receives it and routes it to a supplier who ships the product to the customer. Here, the business doesn’t have to manage an inventory and is free from storage costs while the supplier takes care of fulfillment. The business can spend this freed up resources on other activities like customer support, marketing, etc. It’s one of the growing models, accounting for $300 billion sales every year. Popular eCommerce platform Shopify follows this model and is one of the successful dropshipper with over 2.1 million daily users.
Safety stocking
This means holding a back-up of critical, most-sold stocks, especially during the high-demand period. It helps businesses monetize their stocks in entirety while not facing issues like stock-outs. By accurately forecasting demand ahead, businesses can hold this safety stocking and handle any surge detected. While this inventory management technique can come in handy for many businesses, it can also put you at risk of resource wastage if not properly estimated.
What are the best practices for logistics inventory management?
Traditional inventories and warehouses use most of the techniques above. And there are a few other inventory management techniques that’s not even listed here - consignment management, cross docking, etc.
However, effective inventory management requires more than using the above techniques. So, pairing the techniques with certain best practices could get you the results you expect - be it warehouse handling, distribution, demand planning, or any logistics goal your business wants to achieve.
Forecast demand accurately: Start with data analytics solutions where you could use historical data for advantage to predict the future demand and avoid overstocking or stock-outs.
Automate operations: Utilize automation end-to-end along and enable real-time tracking with the help of RFID tags, QR codes, sensors, etc., and integrate them with the existing inventory management software. This cuts down the time wasted on manual operations while keeping track of every stock and their conditions, alerting you when it needs your attention.
Vehicle routing: Many businesses struggle to get their products across their fulfillment centers or deliver to customers on time. Vehicle routing can ease the workload for fleet management, allowing them to prefer optimized routes. This way, they could deliver on or before time at low fuel consumption. For example, there are tools like ORION that guides fleet drivers and managers with fast, optimal routes based on real-time traffic conditions, road blocks, weather and other scenarios.
Optimizing storage: And finally, strategically placing the items helps to pick and pack easier, reducing your labor load and increasing productivity. How goods are stored in inventory depends on many factors - your order book, warehouse layout and slot dimensions, seasonality, storage constraints, whether you use equipment like levers, trucks, conveyors, etc. Since the supply and demand can be dynamic, it can be hard to stick with one optimal arrangement. That’s where AI and ML based slotting recommendation engines could help. It could even take into account all the above factors and even more—suggesting products that could be stored together as they are frequently bought together.
Benefits of inventory management in logistics
All these techniques and best practices for inventory management make it easier for logistics companies. From reduced wastage to fast response, it has many benefits to offer.
Customer satisfaction: Nothing makes customers happier than when products are available when they need them or when they get delivered on time. They tend to come for more, bringing more sales and revenue.
Timely planning of inventory: Modern inventory planning comes with many complications with many external factors directly impacting them. It becomes manageable with the use of inventory management tools and real-time tracking.
Improves decision making: Logistics managers and workers could make fast decisions when they are armed with data-rich reports on sales trends, future demand, product performance, requirements, etc. Becoming data-driven, they could take proactive steps to maximize inventory turnover and minimize wastage.
Better cash flow: A fair share of the cash flow often gets tied up on unsold inventory or materials and supplies. When inventory gets aligned with demand, you prevent funds getting blocked and only spend on what’s necessary.
Conclusion
Logistics is an integral part of every business, bringing them miles closer to customers all over the world. To find success and strive beyond the competition, it takes executing the best strategies like accurate demand forecasting, end-to-end automation, and optimizing warehouse layout and slotting. All the above discussed techniques could become a strategic advantage, helping with data-driven insights, improving accuracy, and adapting to changing demands.
Maximize the outcomes of your inventory management techniques
To ensure that your inventory management outcomes are consistent, you must get back to basics a little. Start small and start with a small data audit to see how good your historical data is and what use cases they could fuel. This audit requires a blend of data analytics and science, as well as in-depth domain knowledge about logistics. That’s where datakulture could step in, helping you solve your pressing problems with the help of data.
Get the data engineers, scientists, and project managers to work with you and uncover practical solutions for common and uncommon inventory problems.