How to reduce manufacturing costs?
Increasing manufacturing costs can be alarming, which can put your profit margins at risk. We have shared some strategies for reducing manufacturing costs, based on our experience designing solutions for the sector.

Ram
Oct 30, 2024 |
8 mins
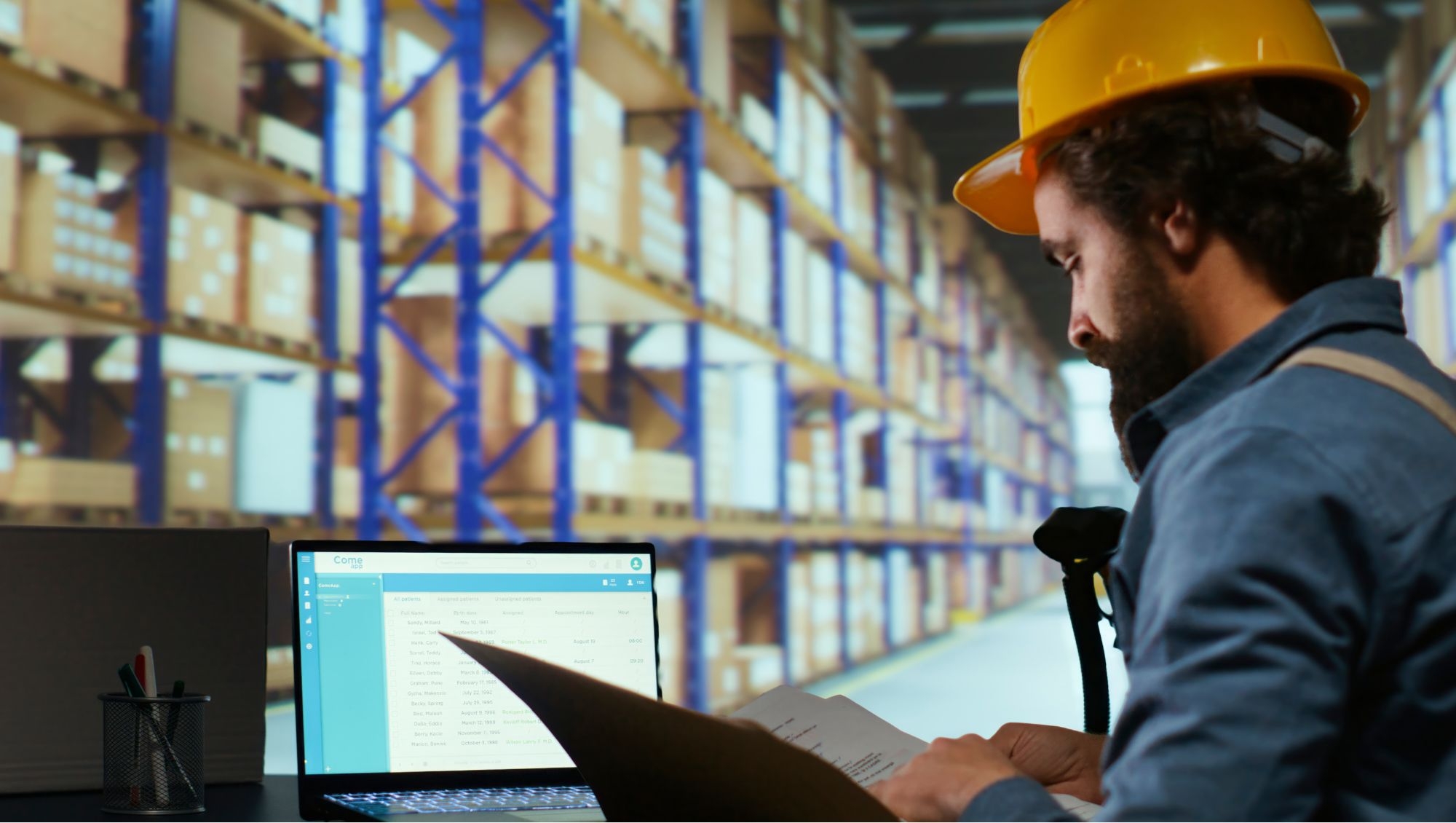
Ways to minimize manufacturing costs
Manufacturing cost denotes the price a company spends to procure turn materials and turn them into products. Each company will have budget and spending restrictions, making the cost rise a burden to handle. There are many reasons behind manufacturing cost rises.
Increase in prices of raw materials, fuel, or labor charges.
Economic factors like Inflations
Geopolitical issues
Maintenance costs, machinery replacements, and upgrades
Port congestion, shipping & freight costs, and other raw material supply chain bottlenecks.
New compliance costs
And many other reasons. Though normal cost fluctuations are common across any industry, it’s important to stay on top of every expense, identify reasons behind, and minimize manufacturing costs.
Inventory management
While controlling manufacturing costs, the best place to start with is smart inventory management. It’s about optimizing operational efficiency while ensuring product availability without overstocking and under-stocking. If you ensure the last one, you could minimize up to 20 to 30% of inventory costs, even with fluctuating raw material prices.
Following are some of the ways to control inventory costs in manufacturing.
Reduce raw material costs by opting for bulk materials, negotiate with suppliers for better prices, minimize waste through lean manufacturing, and implement just-in-time inventory.
Implement inventory forecasting: You could use your historical sales data, seasonal trends, and other operational data to predict inventory requirements for the future. With the help of ML and AI, you could set up manufacturing forecasting, predicting ideal levels of raw materials. No overstocking or under-stocking.
Use tools, technology, and data analysis: you could use ERP systems, inventory management dashboards, and other real-time automated tracking systems. This will ensure that every raw material is used on time, and there is no cost wastage.
Set safety stock levels: safety stock levels can be also based on inventory forecasting. You could receive predictive insights that tell you the minimum levels of inventory stocks required to run operations without facing demand spikes and price increases.
First-in, first-out: use strategies like first-in, first-out for raw materials inventory to minimize wastage due to reasons like aging or expiration.
Supply chain management
Many manufacturers report increasing costs due to supply chain disruptions while sourcing raw materials from vendors. This requires few smart supply chain management strategies to reduce manufacturing costs at any time.
Multi-suppliers: rely on multiple suppliers as this and diversifying vendor base will prevent you from risks and supply chain disruptions. You will not have to face increased material cost and can choose the best deal available.
Vendor relationship management: Track vendor performance, orders, delivery times, and costs in one place using vendor management dashboards. This will open doors to track the best vendors, collaborate with them on more deals, and nurture long-term relationships.
Supply chain traceability: use real-time tracking devices, IoT, blockchain, and other wearables to track supply chain equipment in real time and prevent any fraud or counterfeit.
Go for cost-efficient shipping: there are a few cost effective shipping models available where you can save money. For example, you can go for consolidated shipments, group shipments, etc.
Besides, if your inventory requirements are predicted earlier, you could place orders ahead and go for cost-effective yet slow shipping modes (sea freight).
Use route planning: utilizing AI, ML, and math models, you could receive real-time route planning insights and minimize fuel consumption and labor working time.
Adopting lean manufacturing
Lean manufacturing is a manufacturing concept that focuses on reducing wastage and increasing outcomes. It mainly focuses on continuous improvement and high efficiency, while reducing non-value added things. In short, it’s about delivering the maximum efficiency while using minimal resources, while continuously seeking perfection.
Achieving cost minimization using lean manufacturing
Lean manufacturing aims to address seven types of wastes like overproduction, excess inventory, defects, labor movement, etc., which leads to low-cost consumption.
Lean manufacturing applies the JIT (Just In Time) manufacturing concept, where the materials are ordered and stored, only when there is a production need.
Its continuous monitoring and improvement focuses on quality at every stage, reducing scope for rework and scrap, warranty claims, returns, and wastage, all of which reduce manufacturing costs.
This low-waste manufacturing method also focuses on utilizing laborers to a full extent and improving their productivity. So, a production unit could fulfill its goals with an ideal number of laborers working at maximum efficiency, leading to less labor costs.
Other than this, lean manufacturing aims at reducing fuel and raw materials consumption.
Manufacturing cost analysis
The first step to manufacturing cost reduction is to track the cost related to materials, labor, and other overhead expenses, both fixed and variable costs. This will include calculating manufacturing costs, which involves adding fixed and variable costs.
Fixed costs - expenses that will not change over a period of time, like rent, salary of staff, insurance, etc.
Variable costs - expenses that change every month, like raw materials, contract labors, machine maintenance, and others.
Tracking the above expenses will show you expensive categories where you are wasting your money or resources.
However, tracking isn’t easy for all, especially for companies manufacturing diverse products and a high number of units, dealing with a huge number of accounts payable everyday.
You could use manufacturing cost tracking systems to track real-time and near-real-time expenses, gathering data from all sources. These systems could also measure other key metrics such as activity-based costing, unit based costing, cost-volume profit analysis, etc. modern visualization platforms like Tableau or Power BI come with advanced reporting capabilities, Gen AI options, and what-if analysis features. Using this, you could get further insight and adjust values to see how it impacts production.
All of this will reveal in-depth information about your spending, using which you could develop cost reduction strategies.
Reduce variable costs
Variable costs are the unexpected and changing expenses every company faces once in a while. Some examples include waste, paying shift workers, contract activities, excess inventory costs, and many others. Here are some ways manufacturing companies can reduce variable costs.
Outsourcing non-core activities and choosing contract manufacturing for tedious processes to standardize these costs.
Going for high standards of quality practices like Quality 4.0, a blend of traditional quality methods with advanced digital technologies, to reduce manufacturing wastage and related costs. After all, what is Quality 4.0 if not the future of efficient, cost-effective production?
Conducting energy audits to reduce unexpected hikes in power consumption and switching to energy-efficient, renewable options like LED, solar panels-based equipment, etc. Using IoT devices to track energy, moderate, and stabilize the consumption to reduce one of the expensive variable costs of the industry.
Shift optimization and balanced labor allocation based on predicted demands and machinery uptime for high productivity and moderate labor costs.
Going for inventory and supply chain best practices to reduce high variable costs related to material procurement.
Use the right tools and automate
One of the easiest ways to reduce manufacturing costs is to use automation. It reduces errors, speeds up production, and helps workers focus only on value-yielding tasks, leaving the monotonous ones to automation. Though setting up new tools and technology means a major investment to the company, it could also reduce manufacturing costs the following way.
Allows you to run 24/7 operations, ensuring that there is idle time for machinery and resources, unless you plan a scheduled maintenance.
No repeated tasks, which means minimal labor is required to fulfill the same task. Fewer labors = fewer expenses.
Brings precision and accuracy into the manufacturing process, reducing waste and thereby production cost.
Tools like predictive analytics can predict your load requirements, helping you manufacture in required quantities, leading to optimized storage and on-time supply chain.
The major benefit of automation in manufacturing is fewer cycles and less time for manufacturing, allowing multiple tasks to happen simultaneously and leading to long-term cost savings.
Reduce waste
Waste is one of the most debated topics of the manufacturing industry. According to U.S EPA, the U.S. alone generates 100s of millions of manufacturing waste every year. This is not only leading to money waste, but also remains a hazardous threat to the environment. Through waste and scrap, a company loses its money invested in raw materials, labor, fuel, utility, along with costs required to dispose of them safely.
It’s high time the industry steps up and works against reducing the manufacturing waste following best practices.
Methods to reduce manufacturing waste and relevant costs
Following methods like lean manufacturing and just-in-time inventory that have worked for many companies like Toyota, Intel, Ford, etc.
Going for eco-friendly and sustainable procedures that reduces waste and recycles scrap and used resources, where one could turn scrap into money.
Using predictive maintenance to reduce downtime in manufacturing, predicting its defects, etc., which can prevent costly breakdowns, replacements, etc.
Reducing carbon footprint is necessary for a company to save manufacturing costs, spent on waste, defects, and scrap.
Final thoughts
A quick summary of what’s discussed above: To reduce manufacturing costs, make production more efficient, cut waste, manage resources better, use lean techniques, automate processes, negotiate with suppliers, use JIT inventory, and maintain equipment regularly. Continuously review and improve operations through data-driven decision-making and employee training. Check out our case studies, where we have promoted lean manufacturing through the inventory analysis solution for a consumer goods manufacturer.